Increasing the value of a product is important. Consumers are drawn to the idea of high tech being better than run of the mill technology. To catch the attention and dollars of consumers, the marketing team will often use terms like “Aircraft Grade” or “Medical Grade” to make the ski manufacturers’ offerings more attractive. The idea being, if some material is good enough for the high tech and safety conscious aviation industry, it is going to make the ski products more durable and increase our enjoyment when using this piece of technological wonder.
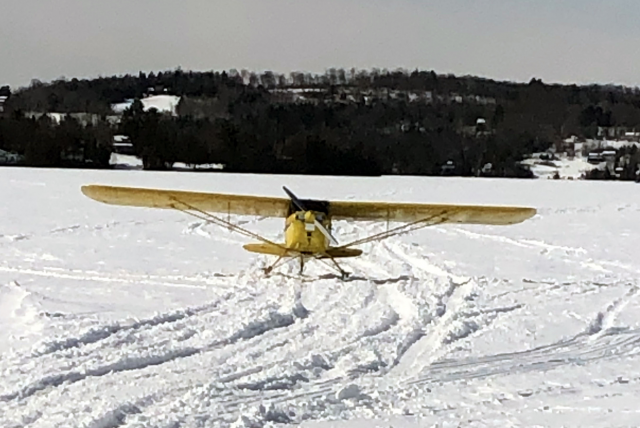
Reversing this trend of taking aircraft grade into the ski industry is a Vermont start-up bringing the nordic ski industry into aviation. For the past five years, the northern Vermont think tank, AlphaQuebec (AQ), has been exploring the use of base structure grinding to improve the takeoff performance of aircraft using skis instead of wheels.
The fundamental problem of skis being slowed down by high moisture snow is the same for both airplanes and skiers. AQ has been investigating ways to make skis slide easier which doesn’t involve waxes or additives. Chief Research Associate, Shelby Taylor explains.
“We know waxes reduce the friction between the base of the ski and the snow. With a nordic or alpine ski you can easily wax the bases. Even a small airplane like a Piper Cub (max weight 1,200 lbs or 550 kg.) you cannot just pop the ski onto a bench and iron on your favorite wax. About three years ago we started experimenting with adding structure to the airplane ski bases. This works great, but again, applying the structure to the bases is not a simple process with the skis attached to the plane.”
Taylor explains that, “Most ski equipped aircraft are single engine bush planes weighing in between 1,200 and 3,500 lbs. (550 to 1,500 kg.) with the largest ski equipped aircraft currently in operation being a military transport LC-130 with an operational weight of 120,000 lbs. (55,000kg.) which is used to supply research stations in Antarctica. Good luck finding a ski form to wax those babies!
“Most of the ski equipped airplanes are used to move people around in snowy environments like Alaska where aircraft are used like an Uber. To keep the economies up and running many areas of the country rely on small, ski equipped aircraft to move people and products. The ground run of a ski plane is slightly longer than the same ship (plane) on wheels. Deep snow is like classic skiing in untracked or wind slabbed junk. You can move but not easily. Just like a skier, the plane sinks in and a lot of space is needed to bring the aircraft up to a speed where the wings develop lift and eventually the skis ride on top of the snow. The plane speeds up and is able to take off. If the snow is high moisture content the ski riding on the surface is slowed by the suction between the ski and the snow. Ground runs can be doubled and its often that there just isn’t enough room to safely take off. Landings can be a problem too because the moisture can grab the ski and act as a sudden brake potentially tripping the airplane and flipping it onto its back.”
We get dressed to spend a few hours outside and drive to the airport testing facility. The airfield feels like a throwback into the mid 1940s. Most of the airplanes were originally built right after WWII when general aviation had a small boom in activity. The airport has several Piper Cubs, a small 2-seat, high wing training airplanes made from steel tubes and covered in Dacron cloth to make them aerodynamic; several Aeronca Champs, a direct competitor to the Cub; Cessna 170 a more modern (these were made in the late 1950s) high wing, four seat all aluminum, and the cutest Taylorcraft, a direct descendant of the Cub with side-by-side seating made just like the Cubs and Champs. Every airplane is equipped with skis. They need to be, the runway isn’t plowed during the winter.
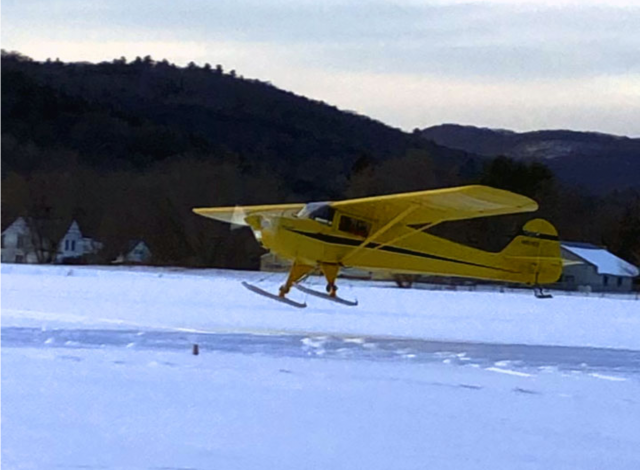
“This is our testing fleet.” Taylor beams with pride. “We have several of the same airplane and therefore are able to test different grinds on each ship. We can load them the same in order to run side by side comparisons in the same snow to see what works the best. You’ve seen wax techs on the test hills holding hands to normalize the in run? We don’t have the airplanes touching for our tests and have the same pilot try the different grinds. This way we remove pilot technique from the data and to the best of our abilities have the only variables be the base grind.”
After the tour of the fleet we entered a large windowless hanger at the edge of the airstrip. “What are all of these?” I ask. Inside is the R&D lab where AQ has been experimenting with driving across waxing and structuring machines. The building is filled with mechanical objects more resembling pallets than ski tuning equipment, most of them less than 12 inches tall (30cm).
“As we discussed earlier, removing a ski to do anything requires a lot of time and work. As a skier, you should remember that not every grind or wax is appropriate for every snow condition.” Taylor replies. “This pile of stuff to our left was the first attempt at having a roller apply hot wax, cool, scrape and brush the skis as the airplane taxied (moves along the ground) across it. Great idea but super impractical. We found some promise with highly fluorinated waxes but obtaining them was difficult. The only reliable source for fluorinated waxes was another small Vermont company, BoxButter, and they were having troubles with the EPA closing the recycling loophole they had been using to bring these waxes to the market.
“It’s a bit ironic in how aviation has dumped literally thousands of tons of fluoros into the environment with the deicing solutions, fire retardant foams, and in the manufacturing of wire insulation for electrical systems. In truth, all of the fluoros used by the ski industry in a year is less than the weight of fluoros used to de-ice just one airliner. You guys were screwed in terms of pinning all of this environmental damage onto the ski industry. We didn’t want any part of the hassle and decided to leave the fluoro debates to others and be able to present a green alternative.
“These taxi across things we called ‘Dial-a-Wax’ and were a cool idea but not marketable. Plus, a fully loaded airplane is going in the 60 to 90 mile-per-hour range (100 to 140 kph) when in contact with the snow so wax didn’t last too long. It’s a good idea but super duper impractical so we turned to the next Holy Grail of ski speed; grinds.”
I follow Taylor through another door. Inside the small room looks like a mechanical horror movie. Strewn all across a dozen workbenches are parts from disemboweled Wintersteiger and Reichman stone grind machines. The next row of benches is filled with structure rollers and enough granite discs enabling the room to pose as a curling supply. Stood up along the walls and held in place by wide elastic bands are dozens of aircraft skis with different colored tags Taylor informs me are used to identify the grind.
“We were able to gather information from national team wax techs by distracting them with cider doughnuts and beer. While they were eating we made rubbings of the ski bases.” My quizzical look invites further clarification. “When you were in grade school did you ever place pieces of blank newsprint on old headstones before rubbing the long side of a crayon to copy the impression? We did this on skis which gives us darker areas which are high and blanks where the base has been ground away. With modern scanning equipment, we gave the density of the color of the rubbing a value, built proprietary algorithms and were able to reproduce the grinds on these granite discs. After we went through all of the trouble rubbing out the bases we got lucky; one of the Scandinavian techs is also a pilot and had just scared the crap out of himself trying to fly back to the home country to grab a pile of skis. When this tech heard about our project he coded the national team grinds and then gave us the entire top-secret binder filled with hundreds of pages of notes. This saved us a lot of crayons, doughnuts, and time.”
She leads me to a table covered in a canvas tarp. Grabbing a corner of the khaki fabric she yanks the cloth leaving it as a pile on the floor next to the bench.
“This,” she says with a lot of enthusiasm “is the Aero-Lift. A method to grind aircraft skis while they are attached to the plane. It’s like a car-wash in that the pilot can sit in the cockpit while a conveyor pulls the skis across the wheels. This is the prototype and it is showing a lot of promise. Sensors out in the field measure the moisture in the snow, air temperature, pyranometer (measures solar radiation falling onto a horizontal surface), humidity, crystal microscopy, and albedo (to determine particulate matter in the snow) and use this information to determine the most effective grind. These algorithms can also predict what grind is most appropriate at different speeds.”
We move to another bench where a contraption resembling an old wooden ladder with PVC pipes as rungs sits idle.
“For those pilots who cannot afford the stone grind, this device, the Structure Ladder, allows them to structure the skis on the move. The benefit is being able to get the structure quickly and easily. It also doesn’t remove any of the base so while it doesn’t work as well its considerably better than nothing at all. Small time operations without the financial resources will just have to accept the lower performance. Just like skis, money makes airplanes go fast.”
Taylor grabs one of the white PVC pipes and pulls it. The pipe isn’t the actual structuring tool but a cover for the rollers beneath it.
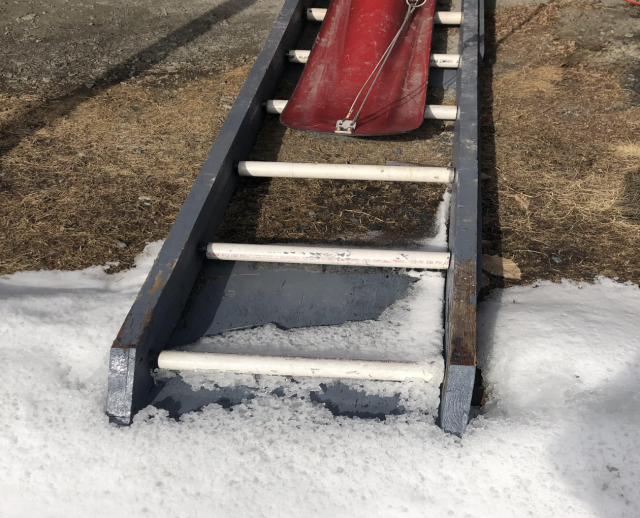
“We have developed a set of structuring rollers each approximately a centimeter wide. It’s mounted on a centering spring so skis with differing arrangements of skegs (longitudinal edges bolted to the underside to help with directional control) can be serviced. The springs keep the appropriate pressure to impress the plastic and push it out of the way so the skegs do not keep the structuring tools off the plastic bases.” NOTE: The springs are undergoing the patent process with some litigation so we were asked to not publish photographs of the actual parts. “Each of these structure ladders contains eight different rollers. Pull the cover for what you believe will work and then just taxi across and just like that you are ready to go.”
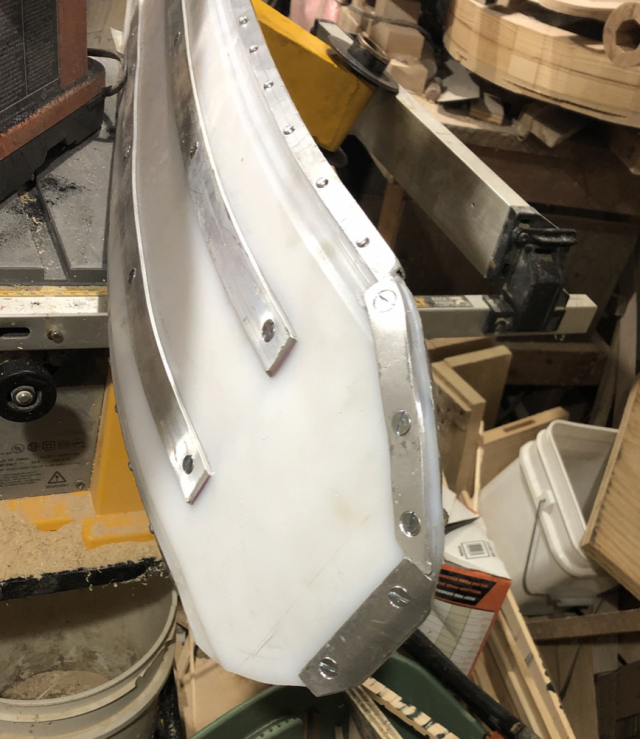
We spend a few more minutes in the R&D room before leaving through a backdoor to go for a flight in one of the AQ test Cubs. The idea of nordic ski technology helping the aircraft industry be safer and more fuel efficient is pretty great but I think it will be a while before Boeing or Airbus brags about the next generation of airliners made with nordic ski grade ideas.
